PRINCIPLES OF SCIENTIFIC MANAGEMENT | FREDERICK W. TAYLOR CONTRIBUTION TO THE THEORY OF MANAGEMENT
Any discussion of the history of modern management thought starts with the ‘scientific management movement’. It was the second phase in the history of management development which saw the rise of the industrial revolution as well as application of scientific management movement. It was the second phase in the history of management development which saw the rise of the industrial revolution as well as application of science of the principles of scientific management .
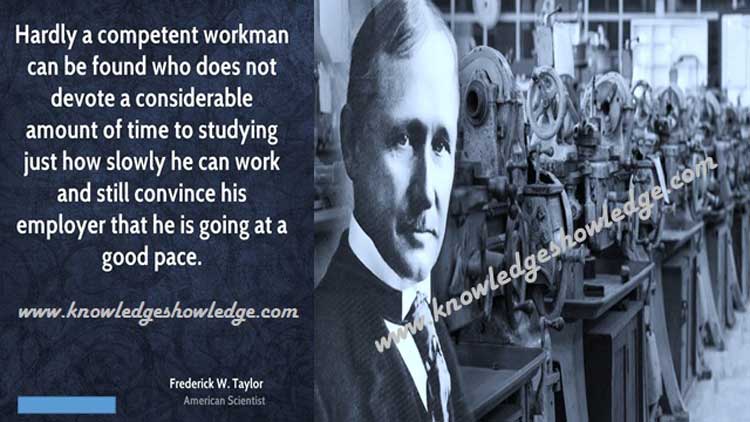
Frederick Winslow Taylor (1850-1915), well-known as the founder of this movement remains the most famous exponent of this approach, having had a worldwide influence for the last half century. Taylor has himself disclaimed credit for founding the movement, but the significance of conversion of board generalizations into practical management tools cannot be easily ignored. He is rightly called the father of Scientific Management.
Starting as an apprentice mechanics in Philadelphia, U.S.A. Taylor rose to be the chief engineer at the Midvale Engineering Works and later on served with the Bethlehem Steel Works were the experimented with his ideas and made the contribution to the management theory for which he is so well-known.
When Taylor entered the industry he saw that management was not aware of scientific techniques of work. The workers were not hard working. He tried to diagnose the causes of low efficiency in industry and came to the conclusion that much of waste and inefficiency is due to the lack of order and system in the methods of management.
He found that management was usually ignorant of the amount of work that could be done by an average worker in a day as also the best method of doing the job. The workers were not selected through any scientific system not they were trained. There was no pre planning for work. No standards were fixed as regards to time and cost of production, etc. So, he suggested the management to adopt a scientific approach in their work and make use of the ‘scientific methods’ for achieving higher efficiency.
Taylor held the view that instead of relying upon the workers to do their job by watching others, the management should condense the great mass of traditional knowledge to a science by, classifying, tabulating and reducing this knowledge to rules, laws and formulas. The following are the salient features of Scientific Management as propounded by Taylor.
“Scientific Management is the art of knowing exactly what you want men to do and then seeing that how they do it in the best and cheapest way.”
Table of Contents
PRINCIPLES OF SCIENTIFIC MANAGEMENT
Scientific management was propounded by Frederick Winslow Taylor (1856-1915) who is the father of Scientific Management Taylor experimented in three companies: Miduale Steel, Semorids Rolling Machine and Bethlehem Steel and on the basis of his observation and findings he has propounded this principle.
There are four principles of scientific management:-
- Science, not the rule of thumb: Taylor has suggested the management as a Every decision to be taken or activities to be performed must be based on facts. He told that we should not stick with old techniques, but strive to form new techniques. The best technique could be found after proper discussion between managers and workers.
- Harmony not discord: He told that inside the organisation, these should be harmony among the workers and there should not be any dispute between the workers.
- Co-operation not individualism: It is extension of that harmony not discord. It states that there should be co-operation among the worker and different departments. Since all departments are interdependent on each other so there should be a spirit of co-operation rather than internal competition.
- Development of each and every one in his/her greatest efficiency and prosperity: Taylor has suggested that the workers and management are complementary to each other. Every worker could be made efficient and expert by properly identifying his talent and giving him opportunities.
When the work done by the workers is productive the organisation will get more profit. Ultimately the workers will also get higher remuneration, resulting them to prosperity.
TECHNIQUES OF SCIENTIFIC MMANAGEMENT
There are following techniques of scientific management:-
- Netted Study: This is the study of finding the best meshed of performing a specific job. While conducting the method study all the responsible factors must be duly considered.
- Time Study: This is the study of finding the standard or optimum time to be taken to perform a given task or to complete an activity. Time study is very useful in management because performance appraisal of the worker can be possible only after knowing the standard time for completing a task.
- Motion Study: This is the study to eliminate or reduce the unnecessary motions of the workers during the work, so that the speed of work can be increased.
- Fatigue Study: This study is to know about the frequency and duration of interval given to worker between the work schedules. Since after continuous work, the workers are tired so rest or interval is necessary to improve their performance.
ELEMENTS OF SCIENTIFIC MANAGEMENT
Scientific Task-Setting
Under scientific management determines the task for every worker through careful scientific investigation. The standard task is the quantity of work which an average worker working under ideal standardized conditions will be able to do in a day. This was called ‘a fair day’s work’. Thus Taylor stressed upon standardization and pre-planning.
Planning
Planning is the heart to Taylor’s idea of scientific management. This planning was concerned with four things: What work has to be done, how it is to be done, where the work shall be done, when it will be done. The first question was to be dealt with by the management and the engineering department.
Taylor advocated the setting up of a planning department. This department will receive detailed instructions and formations relating to the type shape and quantity of products to be produced and the dead line by which the production is to be completed. In planning department four persons were to Work Programme Clerk, Instruction Clerk, Time and Cost Clerk, and A Disciplinarian.
Working Study
It may be defined as the systematic, objective and critical examination of all the factors governing the operational efficiency of any specific activity in work study Taylor stressed on methods study, time study, fatigue study and scientific rate setting.
Methods Study
Under this study, the management must make an overall study of the entire production process. Then management should made efforts to reduce this distance to be travelled by materials during productive cycle, improvements in material handling, internal transportation, etc. On this basis, a ‘Process Chart’ setting out the various operations may be prepared. With the help of such study, the management can try to ensure that the plant is laid out in the best manners and it equipped with the best tools and machinery.
Motion Study
It is study of the movements of an operator (or a machine) in performing an operating for the purpose of eliminating useless motions. For conduction motion studies, workers are studied at their jobs and their all movements are noted. Then they are analyzed and useless motions are eliminated, thus a less time consuming and more efficient system of operations is developed.
Time Study
The purpose of time study is to determine the proper (or standard time) for performing the operation. In the words of Kimball and Kimball, “Time study may be defined primarily as the art of observing and recording the time required to do each detailed element of an industrial operation. “Time study when done with motion study helps in determining the best method of doing a job, determining the standard quantity of one day’s work (standard task to be done by an average worker) and in rating the work.
Scientific Selection and Training of Workers
Taylor stressed on the systematization of selection according to the nature of requirement of job. Having selected the workers the management will assign tasks to them. Every job must be entrusted to the best available man in the factory. Proper attention should be devoted to the training of workers in the correct methods of work. This scientific management requires the prior training of workers before allotting them certain task in the plant.
Standardization
Taylor suggested the standardization of not only production but tools, equipment’s and of working conditions also. He insisted upon the use and store of standard tools and equipment’s in order to get the best production. He advised the management to set an optimum speed for every machine and one best way to do each job. To attain the standard production, he insisted upon the maintenance of standard conditions of ventilation, heating, cooling, humidity, space and safety etc. The use of high quality raw material and good methods of handling materials were also stressed upon.
Differential Piece-rate System of Wages
Taylor believed that financial incentives is the most appropriate incentive because man works for only money. To ensure the efficiency and speed of works he suggested the system of differential piece-rate wages. According to this system two piece-rate were to be determined. One for standard production and other for lower production then the standard limits. It was believed that each worker will try to raise his efficiency in order to get the wages at higher rates.
Functional Organization
Under the traditional plant set up, usually one foreman was given the charge of a number of workers. But Taylor suggested the scheme of Functional Foremanship’ under the scheme, the two functions of ‘planning’ and doing’ the the separated in the organization of the plant. Four foremen will look after the planning work and other four will supervise the work in the shop. Taylor contemplated eight functional foremanship.
Mental Revolution
It involves the change of attitudes on both side. Actually, worker management co-operation may be regarded as the pedestal on which the structure of scientific management can be built. Taylor asserted that all the measures outlined in the system of scientific management will be fruitless until and unless there is a complete mental revolution on the part of both the management and the workers as to their outlook and attitude towards work and towards one another. Taylor advised that the methods of scientific investigations and knowledge must be accepted by both the parties without any mental reservation on their part.
To sum up, “the success of scientific managements rests primarily on a fundamental change in the attitude of management and workers both also their duty to co-operate in producing the largest possible surplus and as to the necessity of substituting exact scientific knowledge for opinions or the role of thumb of individual knowledge.”
CRITICISM OF SCIENTIFIC MANAGEMENT
Scientific management helped in the best utilization of men, machines and material and lead to an improvement in the workers earnings and working conditions. But the whole picture of scientific management is confined to the technological improvement and not in human areas. Scientific management is only a device to speed up to the workers without such regard for their health and well-being. It reduces the workers to the role of an impersonal cog in the machine of production. His job becomes more and more narrowly specialized. It reduces his overall involvement and pride in his job.
As the workers are not given any opportunity to show their initiative and skill and are required to work strictly according to the directions of the foremen. It mars their initiative, introduces monotony in them and workers trade union movement. Thus the approach of scientific management was most inhuman in nature. These all weaknesses of this approach led to the emphasis on human relations in industry.